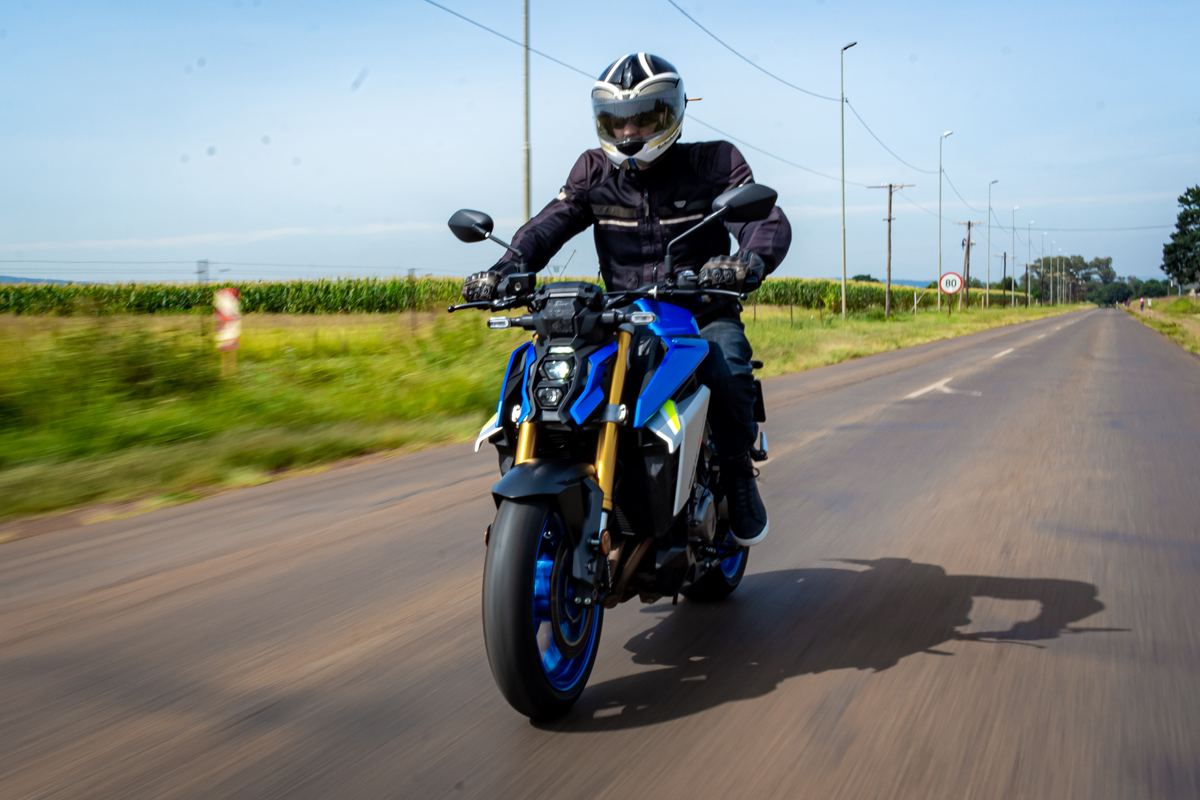
There isn’t a motorcycle importer in South Africa who isn’t always trying to think up new ways of promoting their products in a new and interesting way. Giving new models to journalists is one thing (and not completely ineffective) but that’s the easy way out; trying to come up with something that’s not been done before is slightly more difficult.
Suzuki South Africa put their collective heads together recently to come up with a way of reinforcing the news that the new GSX-S1000 is here and available in Suzuki showrooms countrywide. It’s not a new model but it is one that deserves a bit of trumpeting about, being a valuable entry into the naked sports bike class.
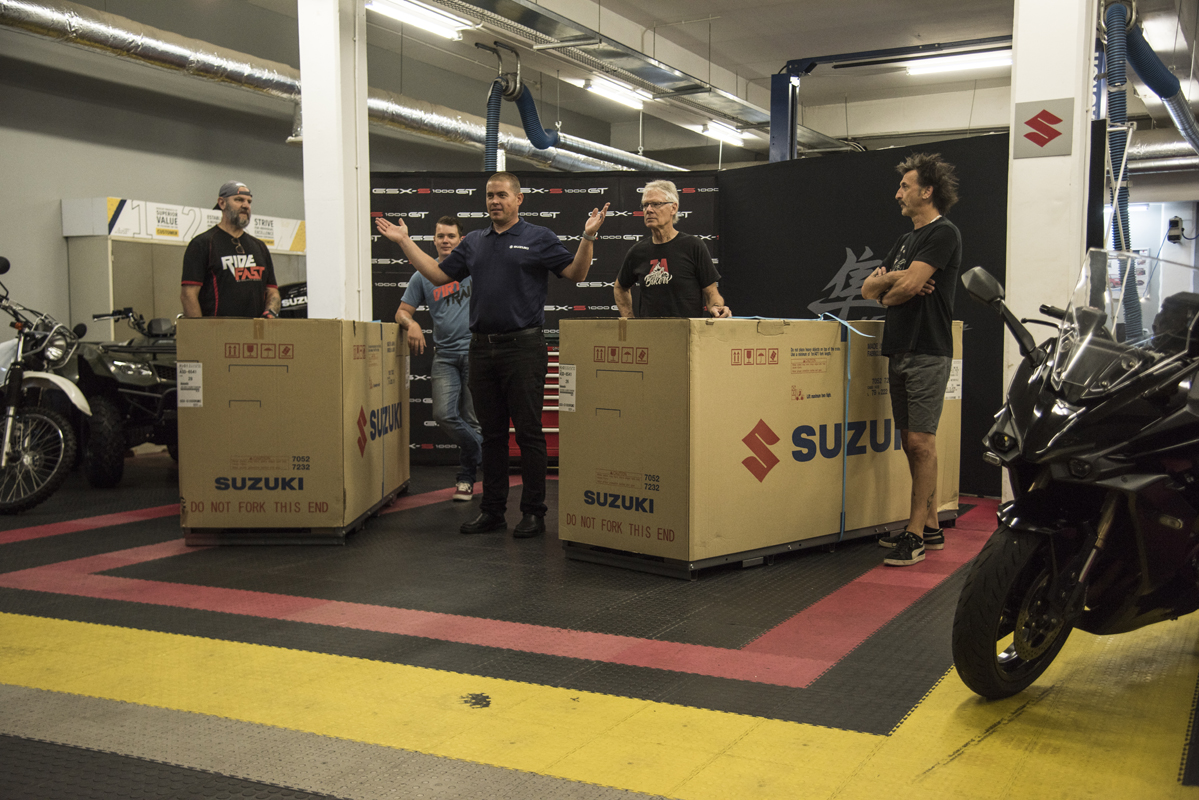
So, what was this novel idea? Basically, it was the decidedly worrying idea of letting journalists loose on two brand new GSX-1000s, still in their shipping crates, and instructing them to get them ready for delivery. Two two-man teams were formed, being from Dirt & Trail/Ridefast magazines and ZA Bikers and we both had a bike to prepare before we would ride them off into the sunset on an extended test.
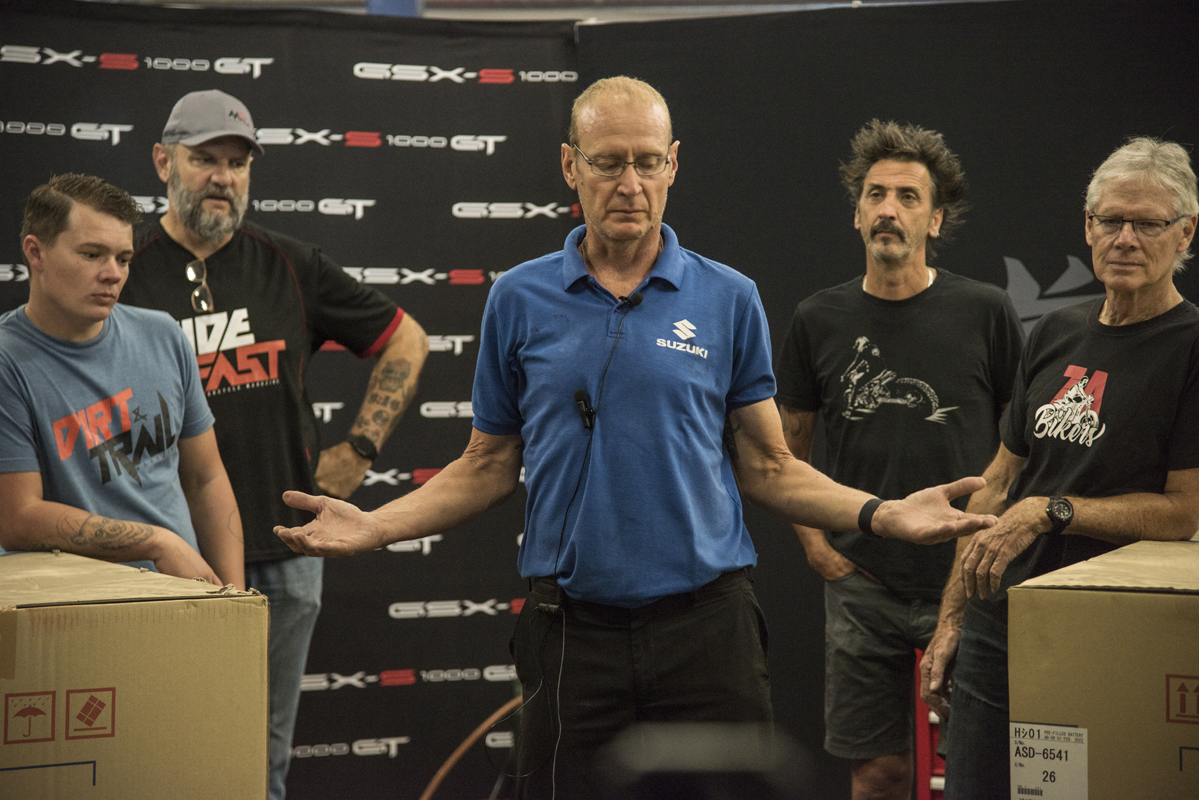
The bikes were in an as-delivered from-the-factory state, which means they were crated virtually complete and needed only the final assembly of handlebars and switchgear as well as various adjustments and checks, such as ensuring the correct torque had been applied to wheel spindle nuts, brake calliper bolts and so on. The battery had to have a quick charge, number plates and licence disc attached, the engines run and then stopped to check the oil level and topped up if necessary. Basically, the process comprised lots of small steps in order to ready the bike for delivery and, according to Doug Lang of Suzuki, should take us no longer than 45 minutes. Easy for him to say!
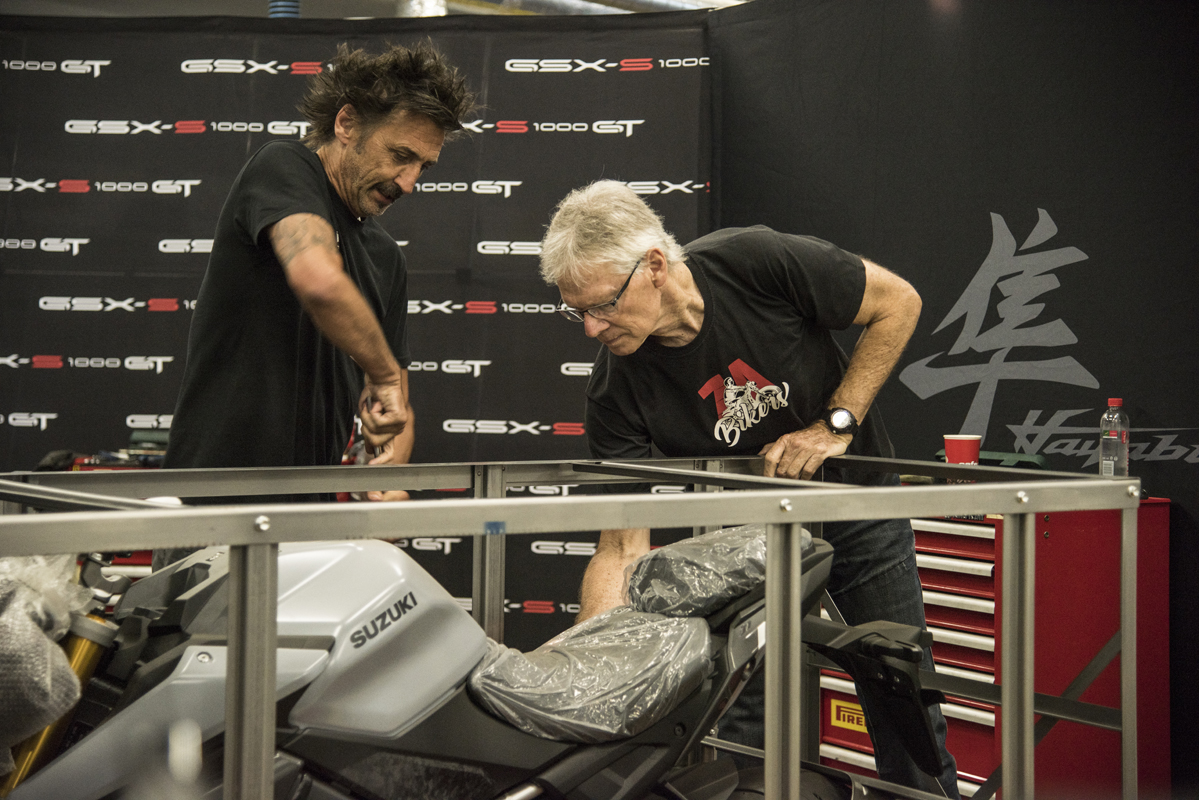
As delivered, the bikes are encased in a framework of steel strips bolted together and a large cardboard ‘lid’. A box nestles within containing assorted nuts, bolts and other small components.
With the clock running, the first task was to remove the cardboard ‘lid’ and disassemble the steel structure encasing the bike. The battery was removed to put on quick charge and then assembly could begin. There was nothing particularly challenging but common sense had to be used and teammates had to coordinate with each other in order to stay out of the other’s way as much as possible.
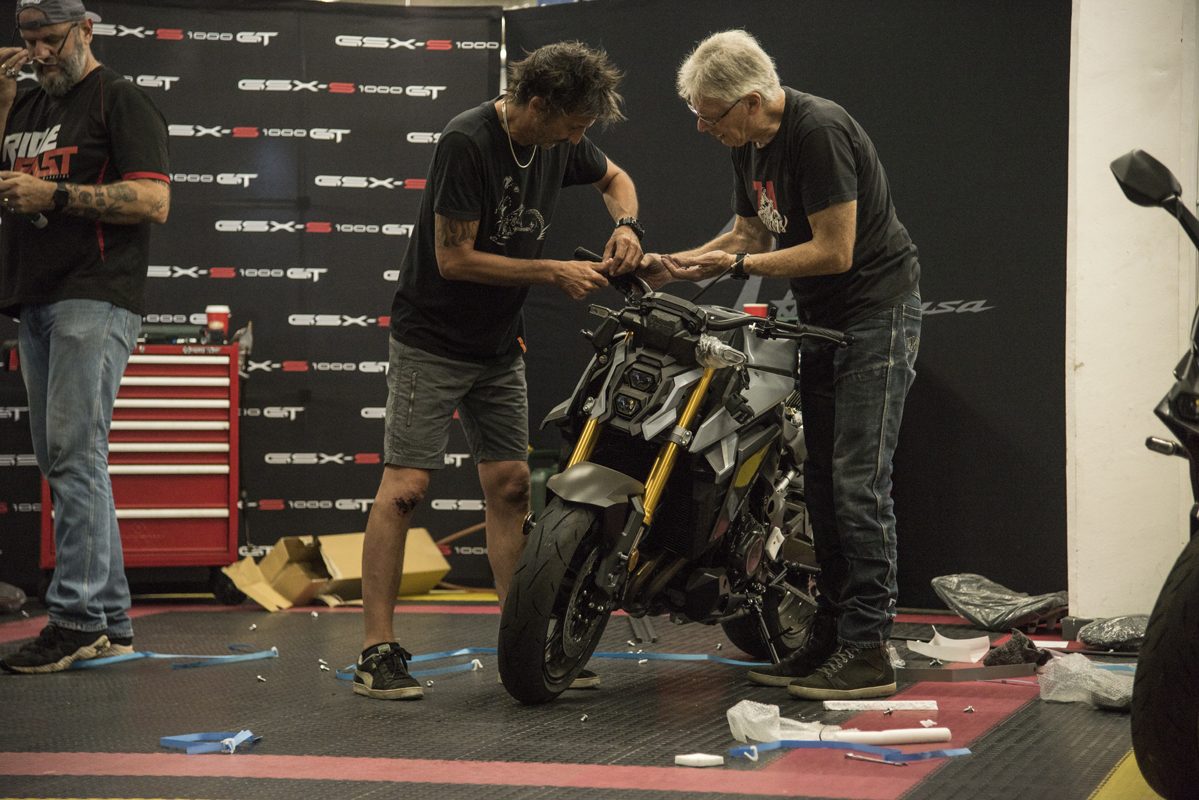
All the handlebar switchgear was hanging loose and had to be assembled on the handlebars before the latter could be bolted to the top triple clamp. The clutch lever was already attached to the ‘bars, but the front brake/master cylinder assembly had to be attached. Affixing the two switchgear pods to either end of the bars proved to be tricky, with two lengths of screws and no indication of which hole took which screw. Trial and error followed: more error than trial, it has to be admitted!
The key thing was to not rush: more haste, less speed, I think the saying goes. Also, as each team was to keep ‘their’ bike for a couple of months, we needed to get it right if we weren’t to inadvertently kill one of our colleagues. Even though it was a race, care had to be taken to get everything right.
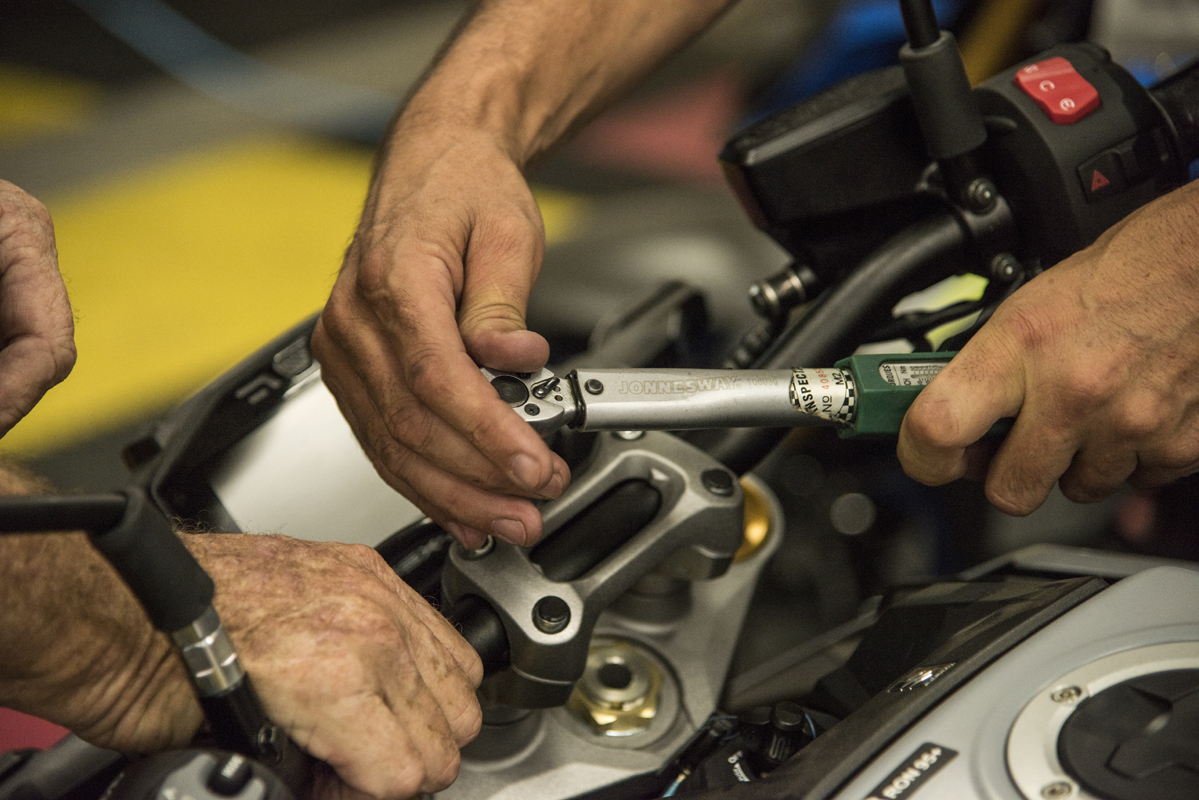
The rear number plate carrier had to be fitted and even the licence disc had to be cut out and clear-taped to the top of the fork stanchion. Handlebar mounting bracket bolts had to be torqued down to the right setting and the torque wrench was also applied to the front brake calliper bolts and the wheel spindle bolts. The brake discs had to be wiped clean with petrol.
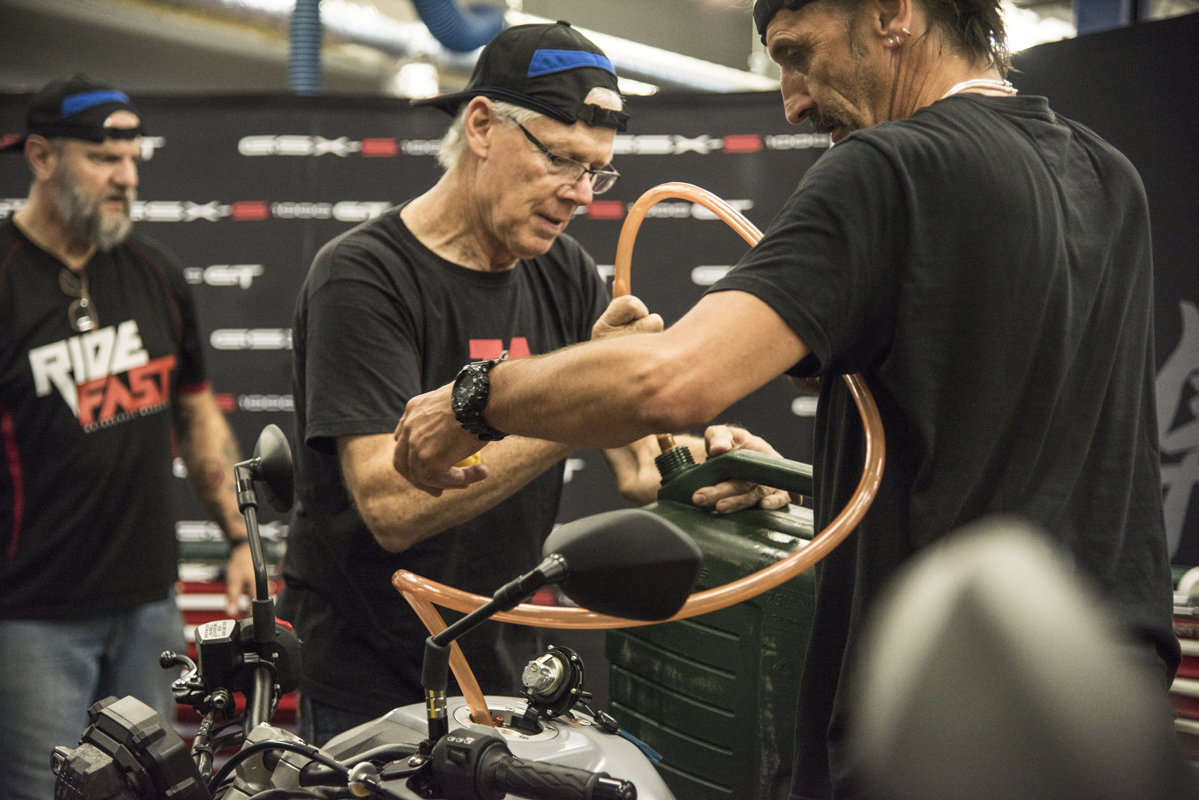
With the bikes together, we could now fit the batteries and fire the bikes up to check the oil levels, as well as the function of lights, indicators, etc. Setting the time and date on the dash was a bit of an issue as we tried to suss out how the mode and adjustment toggle switch worked. Both bikes needed a slight oil top-up.
We got hung up with our dash setup – will any owner ever have to endure the pain of trying to adjust the time and date? Both teams were virtually neck and neck but a tactical move on ZA Bikers’ part pulled back our slim advantage over our rivals. Realising that we could do final adjustments while our bike ran through its start-up sequence, we hit the starter and our bike idled as we finished our final adjustments. The bike needs to idle till the fan comes on at 105 Degrees C, then runs till the engine cools and the fan switches off. If the rest of the assembly is complete and in ship shape, the team that has the fan turned off first wins the shootout. And so it was.
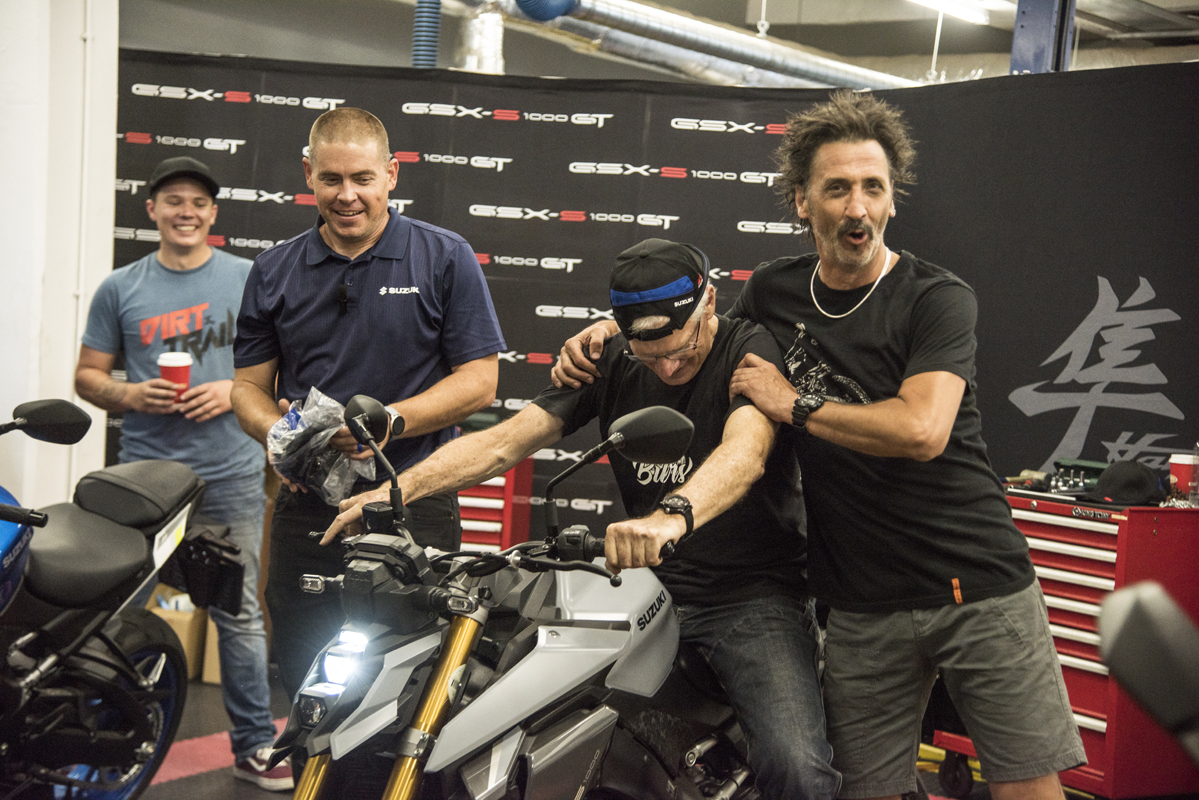
Dirt & Trail/Ridefast were in our slipstream, but with wild jubilation and fist pumps (well, a dignified ‘well done, old chap’) ZA Bikers’ fan cut off literally seconds before theirs! ZA Bikers had prevailed! From start to finish, it had taken an hour and fifteen minutes to assemble and PDI (Pre-Delivery Inspection) the bikes. Doug burst our bubble by telling us that the factory allocates 45 minutes for this task and he did not consider us worthy of employment. 45 minutes sounds reasonable once you know what you have to do before you have to do it.
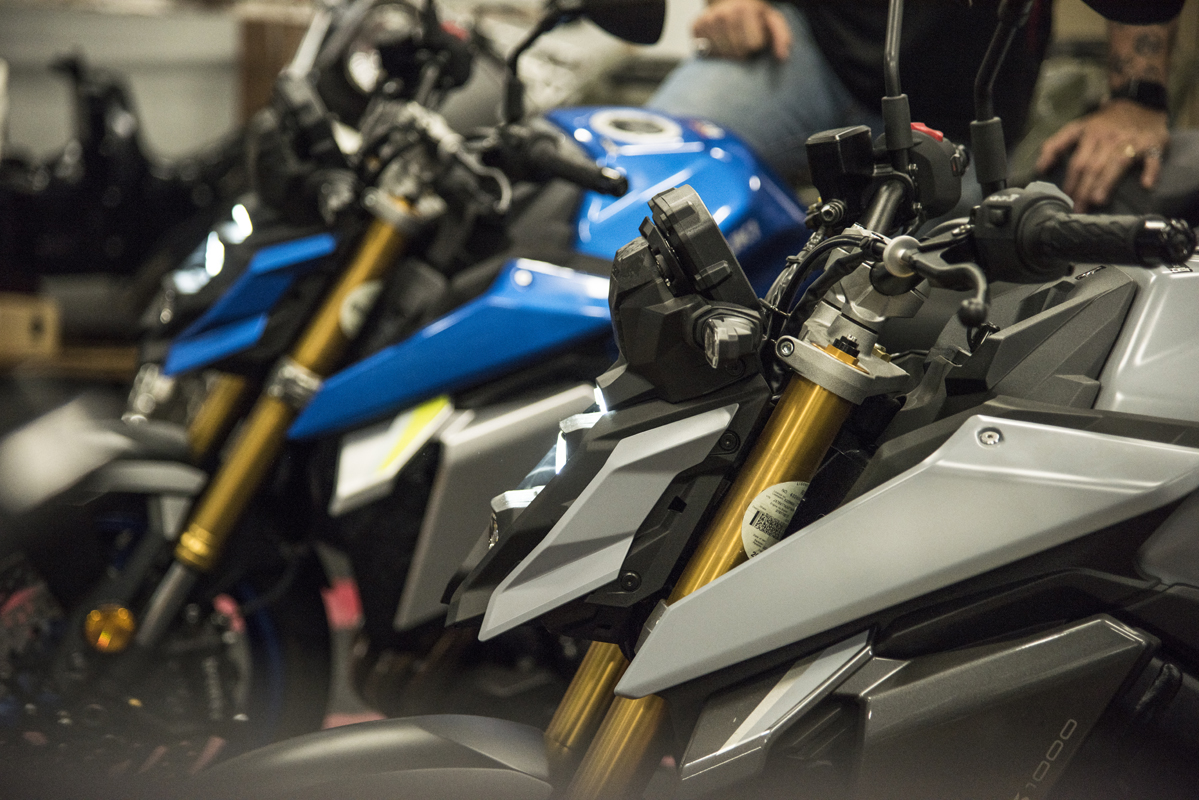
Personally, I would have loved to have been given a deconstructed engine and told to get on with putting it together but presumably, Suzuki wants to sell the bike without a small bag of left-over nuts and bolts that were ‘obviously’ superfluous… As it was, the minimal ‘assembly’ required to prepare the bike for delivery to a lucky customer was a fascinating insight into the logistics facing motorcycle importers, not to mention getting us closely acquainted with what was due to be ‘our’ bike for the next three months.
During this time we will use them as daily rides and give you all the feedback on living with these beauties on a day-to-day basis.
Our thanks to Suzuki SA for a fun and novel introduction to the GSX-S1000. Visit your local Suzuki dealer for more information.
Suzuki GSX-S1000
For more information on the bike featured in this article, click on the link below…